导读
APC已经在炼油、石化、化工、建材、冶金、热电等流程工业得到应用,有效地帮助企业提升了生产效率、产品质量和资源利用效率。本文将介绍流程工业的APC技术及应用,并盘点国内外主要的APC厂商。
作者:e-works研究院 张洋
先进过程控制(Advanced Process Control,APC)是一类区别于常规PID控制的控制策略的统称,主要用来处理常规控制效果不好,甚至无法控制的复杂工业过程控制问题。APC已经在炼油、石化、化工、建材、冶金、热电等流程工业得到应用,有效地帮助企业提升了生产效率、产品质量和资源利用效率。
本文将介绍流程工业的APC技术及应用,并盘点国内外主要的APC厂商。
在此特别感谢中控技术创始人褚健、中控技术过程控制与优化领域专家金晓明两位老师对本文的指导和建议。
01
APC技术简述
1.工业过程控制发展概述控制的历史可追溯至公元前1500年,当时的计时器-水钟已经蕴含了早期的控制思想。时至今日,控制在日常生活中无处不在,家用电器、交通工具、运载火箭、载人飞船都是被控制的对象,应用了控制理论和相关技术。工业过程控制是控制理论在工业生产中的应用,例如对温度、压力、流量、物位、成分等过程量的测量和控制。
工业过程控制主要经历了简单控制、复杂控制和先进控制的阶段。通常将单回路控制称为简单控制,它以经典控制理论为基础,通常采用PID(Proportional-Integral-Derivative,即比例-积分-微分)控制策略。目前,PID控制仍然得到广泛应用,在许多DCS、PLC系统中,均设有PID控制模块或算法软件。
如何理解PID控制?以控制水槽水位为例,比例环节会根据水位和目标水位的偏差大小来调整进水阀门,偏差越大,调整幅度越强;积分环节则考虑偏差的累积,如果水位持续低于设定值,积分作用会使阀门逐渐开大,反之则关小,以消除稳态误差;微分环节则依据偏差的变化趋势,提前做出调整,减少波动和超调。
通常的简单控制主要针对单变量对象,之后陆续出现串级、比值、前馈、均匀、分程、选择性、Smith预估控制等复杂控制系统,不仅实现了对于单变量控制的一些特殊、严苛的控制性能要求,例如减小超调或减少调节时间,而且在很大程度上为实现复杂生产过程多个回路的协作和多个变量的协调控制提供有力支撑。
以管式加热炉的控制为例,在单回路控制系统中,燃料压力或燃料热值变化影响炉膛温度变化,进而将热传导给原料,再根据原料出口温度调整燃料阀门。而在串级控制系统中,通过加测炉膛温度变化,在发生扰动时先通过T2T、T2C回路提前控制(粗调),再通过T1T、T1C回路实现精调,一定程度地增强了系统的抗干扰性,使其能够更快地从扰动中恢复至稳定的运行状态。
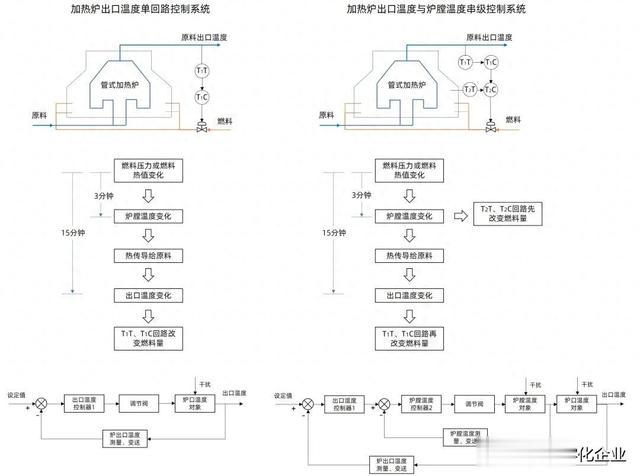
图1 单回路控制系统与串级控制系统举例 (来源:王再英等《过程控制系统与仪表》)
然而,在工业生产过程中,仍有一部分上述控制系统难以解决的控制问题,例如具有大时滞、强耦合、多约束等复杂特性的对象。这些问题往往存在于生产过程的核心环节,直接关系到产品质量、产率等关键指标。
与此同时,随着工业不断发展,尤其是流程工业走向大型化、集成化、连续化、复杂化,对生产过程控制的要求日益提高,增加了更多经济效益、安全管控、绿色节能等指标要求,而传统的基础控制技术难以满足需求,迫切需要一类合适的、更先进的控制策略和技术来解决过程控制与效益指标的矛盾。因此,先进过程控制应运而生并不断发展。
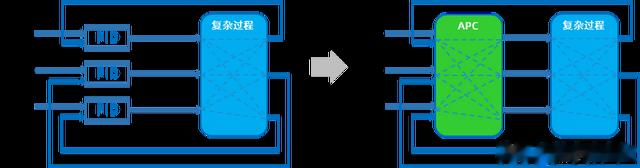
图2 从常规PID控制到先进过程控制
2.APC及关键技术先进过程控制APC是相对于常规控制而言的,能处理常规控制所不能处理的问题的技术,都可称为先进过程控制。作为控制方法的统称,先进过程控制囊括了许多不同的控制技术。
表1 传统控制技术与先进过程控制技术
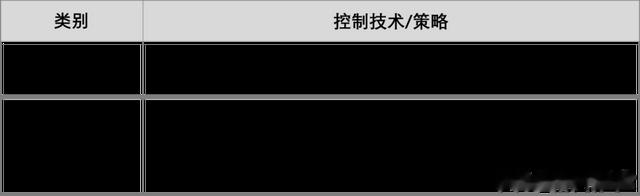
相比常规PID控制,先进过程控制在处理大时滞、多变量、多约束控制问题,实现平稳控制与卡边操作,提升控制系统适应性和鲁棒性等方面具有优势。
表2 传统PID控制与先进过程控制比较
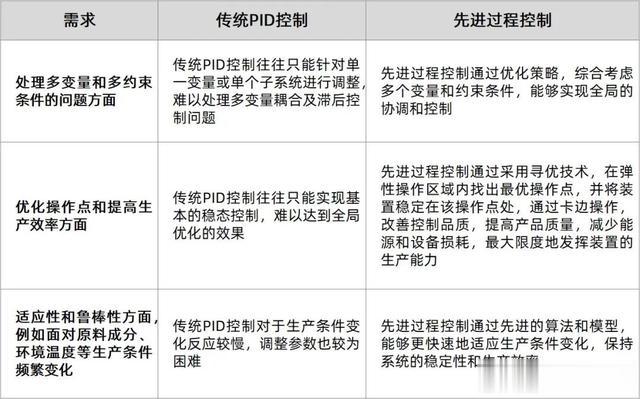
目前,模型预测控制(Model Predictive Control,MPC)应用最为广泛的先进控制策略。模型预测控制是一种基于过程动态模型的控制策略,通过预测模型预估被控变量未来的变化趋势,并以被控变量的当前实测值与上一时刻对当前时刻的预测值之间的偏差,修正对未来时刻的预测,进而提前做出控制决策,优化当前时刻的控制输入。模型预测控制通过模型预测、反馈校正和滚动优化三大核心步骤,使模型失配、外部干扰等引起的不确定性及时得到克服,从而大大改善控制系统的动态性能。
模型预测控制如同汽车的智能驾驶系统,这个系统不仅知道车辆当前位置,还了解前方的路况、交通规则,能够预测未来可能遇到的情况。基于这些预测,系统为驾驶员规划出一条最优的行驶路线,并指导车辆何时加速、何时减速、何时转弯,以安全、高效地到达目的地。
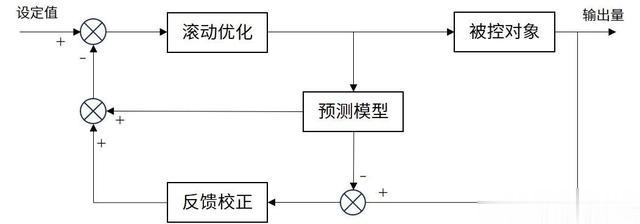
图3 模型预测控制基本原理示意
先进过程控制应用的基础是生产过程的大量实时数据、过程动态数学模型以及先进控制策略。相应地,APC产品一般包括多变量预测控制、软测量、性能评估、建模设计等主要模块和功能。例如,中控的InPlant APC产品包含多变量预测控制APC-Adcon、智能软测量APC-Sensor、性能监控和性能优化APC-Watch、先进控制平台APC-iSYS等。以MPC为核心的APC系统架构可参考下图。
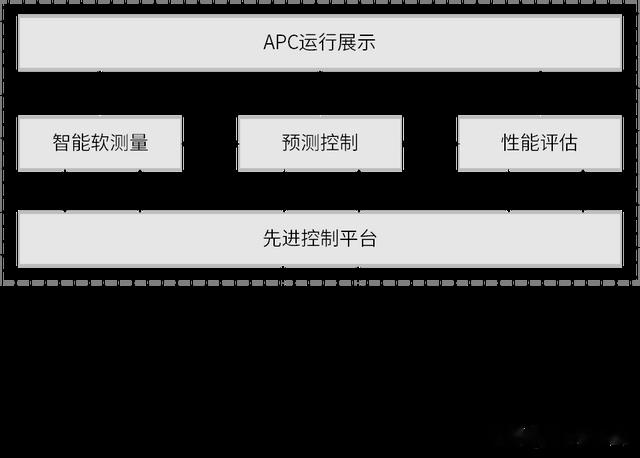
图4 APC软件架构示意
APC系统的硬件架构可参考下图。APC系统通过先进控制软件与DCS上的常规控制器集成,对装置工艺参数全面调节,实现生产过程中多个控制目标。APC并不直接控制仪表和设备,APC与DCS之间通常通过OPC进行通讯,在一定情况下APC和DCS常规控制可以实现互相切换,确保设备安全稳定运行。
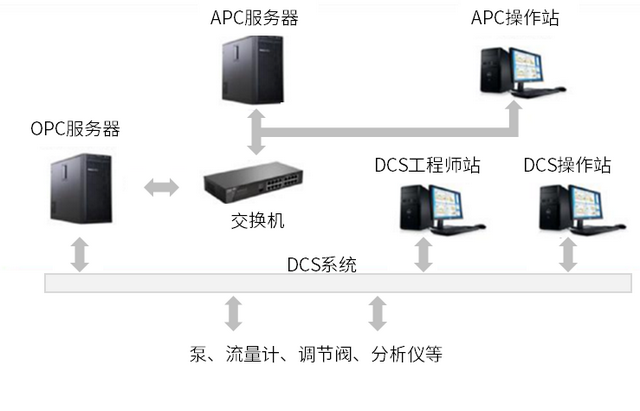
图5 APC网络架构案例
虽然APC可以帮助企业提高生产装置平稳性,实现卡边操作,但是APC需要设定好被控变量的目标值以及工作范围。而借助实时优化(Real Time Optimization,RTO)技术,通过工艺机理模型和全流程模拟,可以为APC提供被控变量的优化目标值和操纵变量的理想静态值等参数,使装置在不同负荷和不同生产方案下,都能保持在优化运行状态。因此,“APC+RTO”这一组合在过程控制领域经常被提及。
例如,在乙烯裂解过程中,APC负责监控和控制裂解炉的炉管出口温度COT、精馏塔灵敏板温度等关键变量,确保操作的稳定性和产品的一致性。同时,RTO分析原料质量、原料成本、设备性能等数据,实时调整操作策略,以最大化烯烃收率和整体效益为目标,给出COT温度、灵敏板温度等的优化目标值等。
“RTO+APC”相结合的典型流程行业分层过程控制结构图如图6所示。
RTO层:根据上层给出的物料价格、生产工艺等参数来周期性地优化出一个目标函数,将其计算出的变量优化值作为APC中关键变量的设定值。APC层:通过APC实现过程控制的最优调节,同时完成紧急情况响应和诊断等工作。常规控制层:通过DCS/PLC等自动控制系统实现工业装置的数据获取、错误检测、常规控制和性能监控。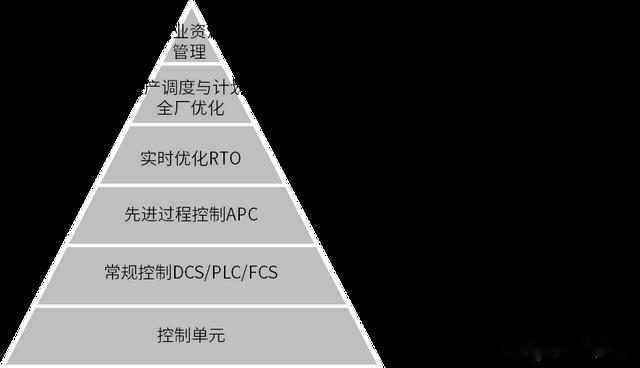
图6 APC和RTO在不同空间尺度的优化和优化周期
3.APC发展方向先进过程控制APC是一类基于数学模型的高级控制策略和技术,涉及运行数据的采集分析,工业运行模型的辨识和建立,以及控制策略和算法的优化。从技术层面来看,APC与人工智能、工业大数据等新一代信息技术融合发展趋势日益显著,新技术的引入也为APC技术发展提供了新的思路和方法。
例如,AI可以用于识别系统的复杂行为,辅助发现生产过程中隐藏的模式和关联,用于设计和优化控制器;强化学习可以应用于控制系统的参数寻优,提升智能控制算法的性能。
借助工业大数据技术,可以获得丰富的历史数据和实时数据,利用数据分析辅助知识挖掘,帮助APC更加准确地描述系统的动态特性和约束条件,从而设计出更有效的控制器。
02
APC应用现状
1.APC应用概述国外在上世纪70年代末、80年代初就开始流程工业先进过程控制技术的商品化软件开发,并在上千家大型炼油、石化、化工、冶金等企业中应用。在石化行业,美国、西欧、日本等发达国家超过半数以上的生产装置实施了先进过程控制技术,美国超过90%的重点装置(例如常减压蒸馏、催化裂化、延迟焦化、加氢裂化等)普及了先进过程控制。
国内较晚开展APC项目的应用和实施。国外先进控制软件于1992年在齐鲁石化的催化裂化装置上首次成功投运。随后在90年代中期,国外先进控制软件公司开始进入中国,快速占领市场。2000年初,仅中石化就先后实施了近百套APC,但主要以艾斯本(AspenTech)、霍尼韦尔(Honeywell)的软件产品为主,费用高。
虽然国内的高校、研究机构和企业从上世纪80年代开始研究先进过程控制理论和技术,并在90年代将预测控制、模糊控制等先进控制技术应用于一些复杂工业生产过程,但是在商业化产品的开发与应用方面与国外存在较大差距。从90年代中后期开始,中控技术公司、浙江大学等结合多年理论和技术积累,开展相关工程化产品的研究和开发,并与国外公司合作,快速借鉴和吸收国际上的先进技术,逐步形成了一批商品化软件,并在炼油、石化、制药等多个大型企业的关键设备中获得实践应用。
目前,APC已经成功应用于国内多个流程行业,覆盖炼油、石化、化工、原料药、冶金和热电等多个行业的几十种典型流程化生产装置。
炼油行业:常减压装置、催化裂化装置、连续重整装置、加氢裂化装置、加氢精制装置、延迟焦化装置、气体分馏装置。石化行业:乙烯装置、芳烃联合装置、芳烃抽提装置、烷基苯装置、分子筛脱蜡、苯乙烯装置、PTA装置、聚丙烯装置、聚乙烯装置。化工行业:纯碱装置、氯碱装置、合成氨装置、氟化工装置、电石炉装置、有机硅装置、多晶硅装置、甲醇装置、硫酸/磷酸装置。其它行业:锅炉、空分装置、硬质合金反应过程、煤气混合过程等。2.APC应用案例先进控制系统的应用可以改善过程动态控制的性能、减少过程变量的波动幅度,使之能更接近其优化目标值而将生产装置推向更接近其约束边界条件下运行,最终达到增强装置运行的稳定性和安全性、保证产品质量的均匀性、提高目标产品收率、增加装置处理量、降低运行成本、减少环境污染等目的。
例如,在石化行业,中国石油化工股份有限公司镇海炼化分公司研发裂解炉裂解深度控制与实时优化软件(APC+RTO),RTO根据原料质量、裂解炉运行周期、价格体系等变化自动计算优化值,APC自动执行调整,在装置总投料负荷不变的情况下,年节约7190余吨标准煤;中国石油天然气股份有限公司独山子石化分公司开发乙烯装置APC先进控制和RTO实时优化系统,裂解深度调整更加及时准确,乙烯、丙烯收率分别提高0.2%和0.1%。
在煤化工行业,神化包头煤化工公司在聚乙烯和聚丙烯装置上引进APC系统,应用于反应器自动控制、循环气组分控制、产品性能计算和产率控制等重要生产单元,大幅提高了工艺生产控制的自动化程度,并实现聚合反应转化率、产品质量、产率的提升。
在冶金行业,鞍钢鲅鱼圈分公司在三座转炉中应用转炉自动化炼钢过程控制系统,实现氧枪过程控制自动化、下料自动化、副枪自动化、冶炼终点抬枪自动化的“一键式”炼钢,实现转炉冶炼初始条件精密感知,实现冶炼过程控制稳定,碳温双中命中率达到 90.4%,稳定控制并最大限度降低钢液终点氧,提高初始钢液质量。
在热电行业,浙江巨化热电有限公司对其 #8机组锅炉控制进行优化。APC改造投运后,风机自动调节,锅炉风机电耗下降,同时锅炉主蒸汽压力、温度更加平稳,波动幅度减小明显,提高了锅炉的安全、经济运行水平,锅炉效率提高0.3个百分点。
在水泥行业,陕西某水泥熟料生产线窑通过实施APC系统,明显降低操作人员的劳动强度和误操作可能,消除操作人员水平的差异,保持操作的一致性,降低烧成工序关键被控变量的标准差40%~70%,有效提高系统的稳定性,并降低熟料工序标准煤耗2.22%和熟料工序电耗1.55%。
3.APC应用挑战相比传统PID控制,先进过程控制确实具有明显优势,值得被推广和应用。但是,同样需要关注的一个问题是APC的应用难度不小。
首先,在典型的ERP/MES/PCS 三层结构中,APC与DCS/PLC一起被划分为PCS层,视为生产控制层面的系统,与DCS/PLC等底层控制系统会进行紧密的集成和协同。其次,APC还涉及到工艺原理、机理建模等多个方面,需要深入理解工业过程的物理和化学原理,以及各种操作变量之间的关系,对人员的专业知识和实践经验要求非常高。而且,APC的有效运行高度依赖于模型,但工业过程往往具有大量不确定性、非线性、多变量耦合、大滞后等特征,建立精确可靠的动态模型十分困难。此外,受环境变化、设备性能退化等因素影响,控制器模型的性能会发生变化,模型参数需要不断修正和完善。综合以上因素来看,APC的应用、维护面临较大的挑战。
03
主流APC厂商巡礼
1.国际厂商根据e-works不完全统计,比较知名的提供流程工业相关APC产品和技术的国际厂商有12家,分别来自于美国、德国、日本、瑞士、英国、丹麦,大部分是仪表与自动化控制领域厂商。除了独立的厂商之外,如埃克森美孚、壳牌等大型企业也建立了自己的先进过程控制项目实施队伍及先进过程控制系统维护团队。
收购和兼并是国际工业自动化厂商扩张和转型的一个重要手段。APC领域同样发生了多次收购。例如:
1995年底,霍尼韦尔收购Profimatics,霍尼韦尔提供RMPC算法与Profimatics PCT控制器合并,推出RMPCT产品。1996年初,艾斯本收购Setpoint(旗下有IDCOM-M、SMCA)和美国DMC公司(旗下有DMC),随后于1998年收购加拿大Treiber Controls公司(旗下有OPC),艾斯本将SMCA和DMC技术被合并,推出了DMCplus产品。2021年,艾默生收购艾斯本55%的股权。2014年,施耐德电气并购英维思(旗下有SimSci-Esscor),后者曾收购美国Foxboro公司(旗下有Connoisseur)。2017年施耐德电气收购AVEVA剑维软件约60%股权,2023年1月施耐德电气完成对AVEVA剑维软件100%的并购控股。2016年,罗克韦尔自动化收购MAVERICK Technologies。表3 国际APC厂商
(e-works整理,按厂商名称英文首字母排序)
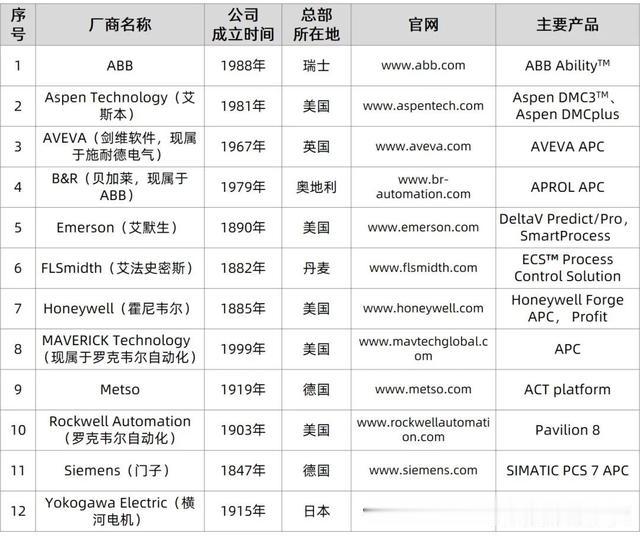
我国的工业自动化领域发展起步较晚。在上世纪90年代之后,清华大学、浙江大学、上海交通大学、东北大学等高校逐渐开发出功能强大的先进控制软件。这其中先后发展了中控技术、清云智通等厂商,另有一批厂商起源于中石油、中石化的子公司,以及国外厂商在国内的合作伙伴。但整体上看,相比于MES、DCS、PLC领域,国内APC市场参与者数量偏少。根据e-works不完全统计,国内有21家提供流程工业相关APC产品和解决方案的厂商。
表4 国内流程工业APC厂商
(e-works整理,按厂商名称拼音首字母排序)
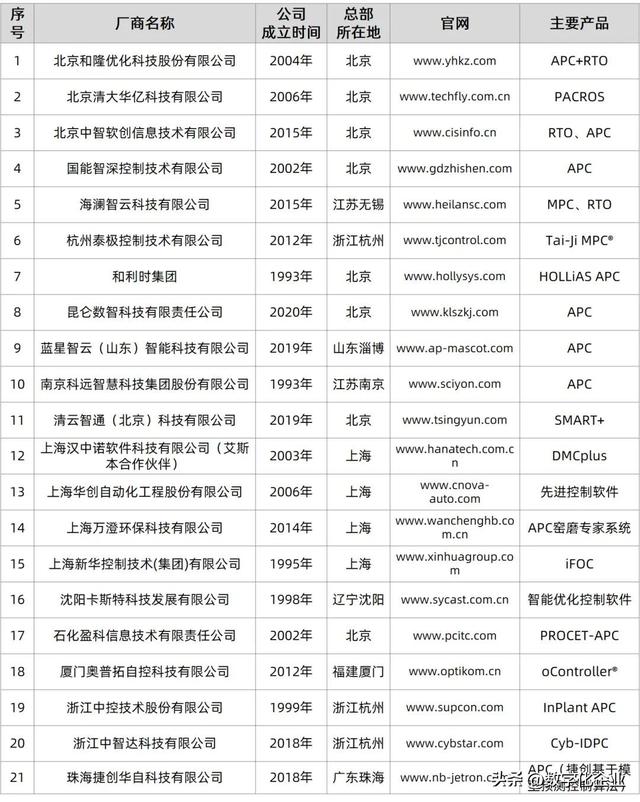
中控技术是国内最早推出APC产品且处于领先地位的APC厂商,截止2022年,其InPlant APC 已在石化、化工、电力和冶金等行业的生产装置上应用超过 1000 套。和隆优化是国内流程工业“APC+RTO”控制技术专业服务商,主要为冶金、热电、化工、水泥行业提供解决方案和服务,在冶金工业窑炉及热电锅炉智能优化控制市场占据优势。石化盈科与艾斯本、霍尼韦尔以及中控技术合作,为中石化APC/RTO装置提供运维工作,公司也有自主知识产权的通用先进控制软件PROCET-APC,在常减压、催化裂化、重整等装置得到成功应用;昆仑数智是中石油的子公司,主要为石油化工行业提供先进控制与优化应用。和利时HOLLiAS APC应用于化工精馏塔、热电锅炉、水泥等行业。
04
总结与展望
当前,我国制造业在发展过程中需要进一步解决能耗偏高、资源消耗量大、产品附加值较低、环境污染较严重等问题。而APC的目标和作用是优化过程控制系统的稳定性、准确性等性能,提高产品质量和生产效率,降低能耗和成本,在推动企业实现制造过程的高效化、绿色化方面,其赋能作用显著。
放眼未来,针对未来的工业制造,有专家学者提出“智能自主控制系统”、“类似自动驾驶的过程自动化”的设想。可以期待,未来工业过程控制系统将变得更加智能化,能够应对更加复杂多变的过程控制挑战,并通过融合人工智能等新兴技术,它们将具备更加强大的自主学习能力,实现更高水平的智能化决策和运行。
说明:文中厂商的盘点由e-works基于公开信息所得,若有遗漏,欢迎与e-works联系补充(zy@e-works.net.cn),谢谢。

[1] 王再英等.过程控制系统与仪表[M]. 北京:机械工业出版社.
[2] 浙江中控软件技术有限公司.国产先进控制软件的开发、应用与前景展望.自动化博览, 2012,29(12):34-37.
[3] 化工装置实时优化系统值不值得?
https://mp.weixin.qq.com/s/lpjEsE7Ncxe3XhuvNhzIIQ
[4] 金晓明,褚健.先进控制技术及其应用[J].世界仪表与自动化, 2001(9):10-15.
[5] 赵恒平.中国石化先进过程控制应用现状[J].化工进展, 2015, 34(4):930-934.
[6] 黄德先.化工过程先进控制的发展过程、国内特殊问题的解决和展望[J].化工自动化及仪表, 2023, 50(5):597-610.
[7] 先进控制技术在流程工业中的应用.
https://mp.weixin.qq.com/s/5L2u1Tr2IOYELRWZ83KTlA
[8] 工信部:《2022年重点用能行业能效“领跑者”企业典型经验与实践案例(乙烯行业)》.
[9] 郭永增,李亦方.APC在煤化工聚烯烃装置中的应用[J].能源与节能, 2015(11):153-155.
[10] 李立勋,田勇,史页殊,等.冶金工艺先进过程控制系统定义高品质钢材生产[C].第十一届中国钢铁年会论文集——S18.冶金自动化与智能管控.2017.
[11] 祝路平,毛双华,林国辉.APC先控在浙江巨化热电有限公司#8机组的运用[J].自动化博览, 2019(7):88-94.
[12] 徐立东,杨宏兴,郭军锋,等.AVEVA APC系统在水泥窑烧成系统中的应用[J].化工自动化及仪表, 2022,49(5):638-643;668.
[13] 柴天佑,刘强,丁进良,等.工业互联网驱动的流程工业智能优化制造新模式研究展望. 中国科学:技术科学, 2022,52:14-25.
[14] 金晓明.过程自动化系统的发展现状与展望[J].化工自动化及仪表, 2024,51(1):1-9.